Three separate, yet intertwined projects
Von Gahlen’s footprint can be found at three different locations throughout this fascinating facility. We therefore distinguish between Amsterdam UMC (location VUmc) and BV Cyclotron VU. Two organizations with distinctive tasks within the Imaging Center. Nevertheless, those tasks are strongly connected. We sat down for an interview with three of our contacts whom we closely cooperated with during the realization of the Imaging Center. We would like to introduce you to Maria Vosjan, Operations Manager at BV Cyclotron VU, Bert Windhorst, professor in radiopharmaceutical chemistry at Amsterdam UMC (location VUmc) and his team member Robert Schuit, Research Technician at Amsterdam UMC (location VUmc). Each of them “represents” a stakeholder from one of the three separate projects Von Gahlen realized within the Imaging Center.
They explain:
- Which radiopharmaca will be produced at the Imaging Center;
- How Von Gahlen built tailor-made solutions to facilitate this;
- How they look back on their cooperation with Von Gahlen.
At the source
BV Cyclotron VU is located in the basement of the Imaging Center; the office of Maria Vosjan. Here, in massively shielded bunkers, four particle accelerators (cyclotrons) generate radionuclides. These radionuclides are used by BV Cyclotron VU to produce radiopharmaceuticals and radiochemicals for their customers. Furthermore, a second important part of these radionuclides are used higher up in the building, on the third floor of the Imaging Center, where Bert and his team are performing routine and experimental production. Von Gahlen built the bunker doors to access and safely close the separate bunkers where the cyclotrons operate. To integrate these doors in the building strong cooperation with the architect and the construction company was key. Maria Vosjan reveals a remarkable aspect of the bunker doors. “We needed Von Gahlen to build quite a specific design. The space is limited, so the doors need to open in a 45 degrees angle.” The picture below shows you the result of this challenging design.
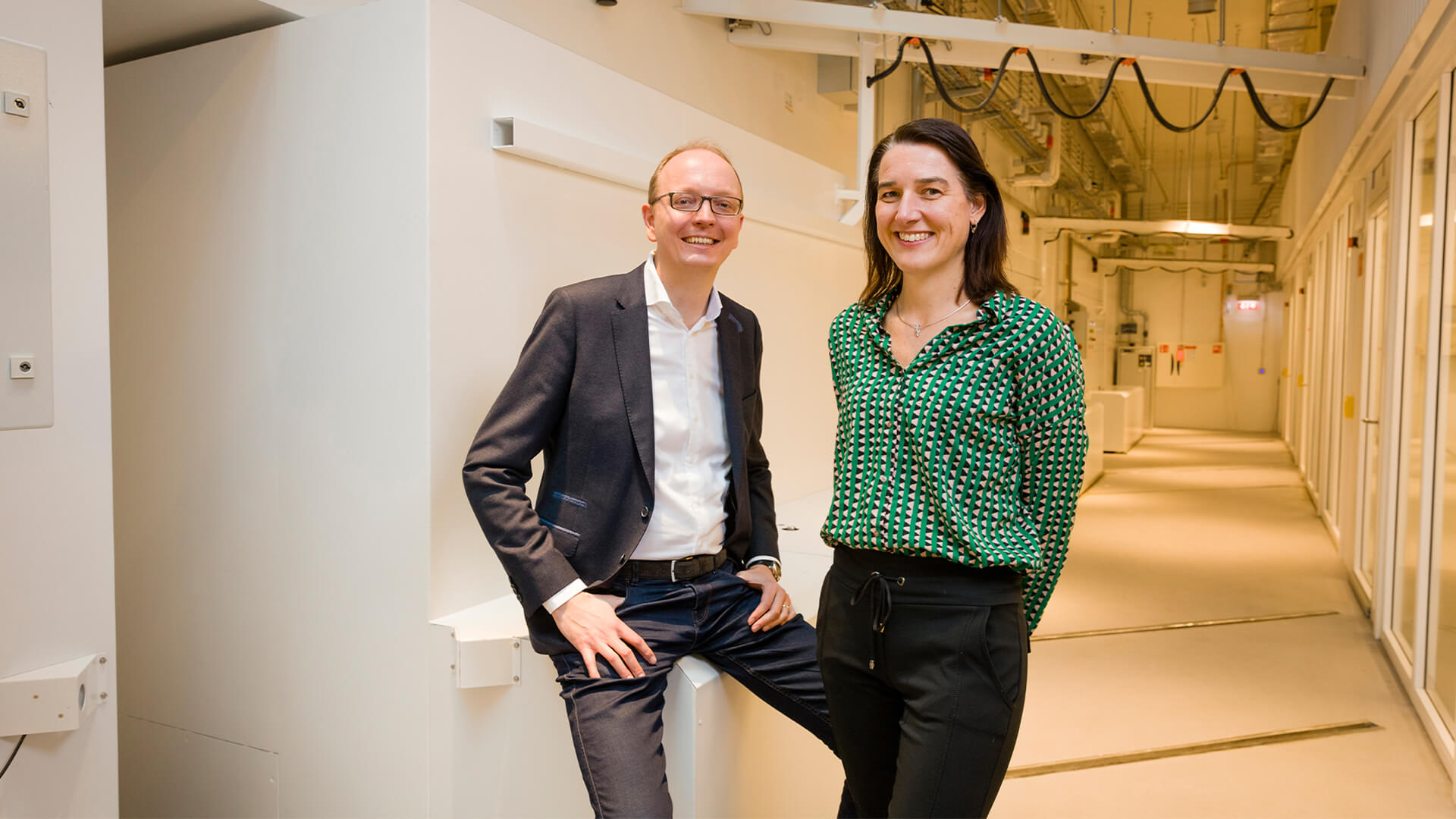
Maria Vosjan of BV Cyclotron VU and Von Gahlen’s Alex Duiker in front of the massive bunker doors, built by Von Gahlen.
Short-life radiopharmaceuticals demand fast handling
Von Gahlen designed and realized four production lines for the several radiopharmaceuticals BV Cyclotron VU produces. Each production line consists of a stacked synthesis hot cell, a single synthesis hot cell and a dispensing hot cell. The dispensing hot cell is connected to a tailor-made output hot cell. This cell enables BV Cyclotron VU to do an extremely fast output and packaging of the product with ‘Type A packaging’ that we specially developed. We also integrated a conveyor belt to quickly transport the packed substances that leave the output hot cells. “Von Gahlen managed to integrate their standard synthesis and dispensing hot cells within customized output hot cells and a well-designed conveyor belt. This enables us to process vials within a very short timeframe”, says Maria.
In order to build such a project from scratch, the Von Gahlen engineers and projectmanager closely cooperated with BV Cyclotron VU and their construction team. In addition to the bunker doors and the hot cell suites as mentioned above, Von Gahlen also delivered two shielded laminar flow hoods and four shielded fume hoods.
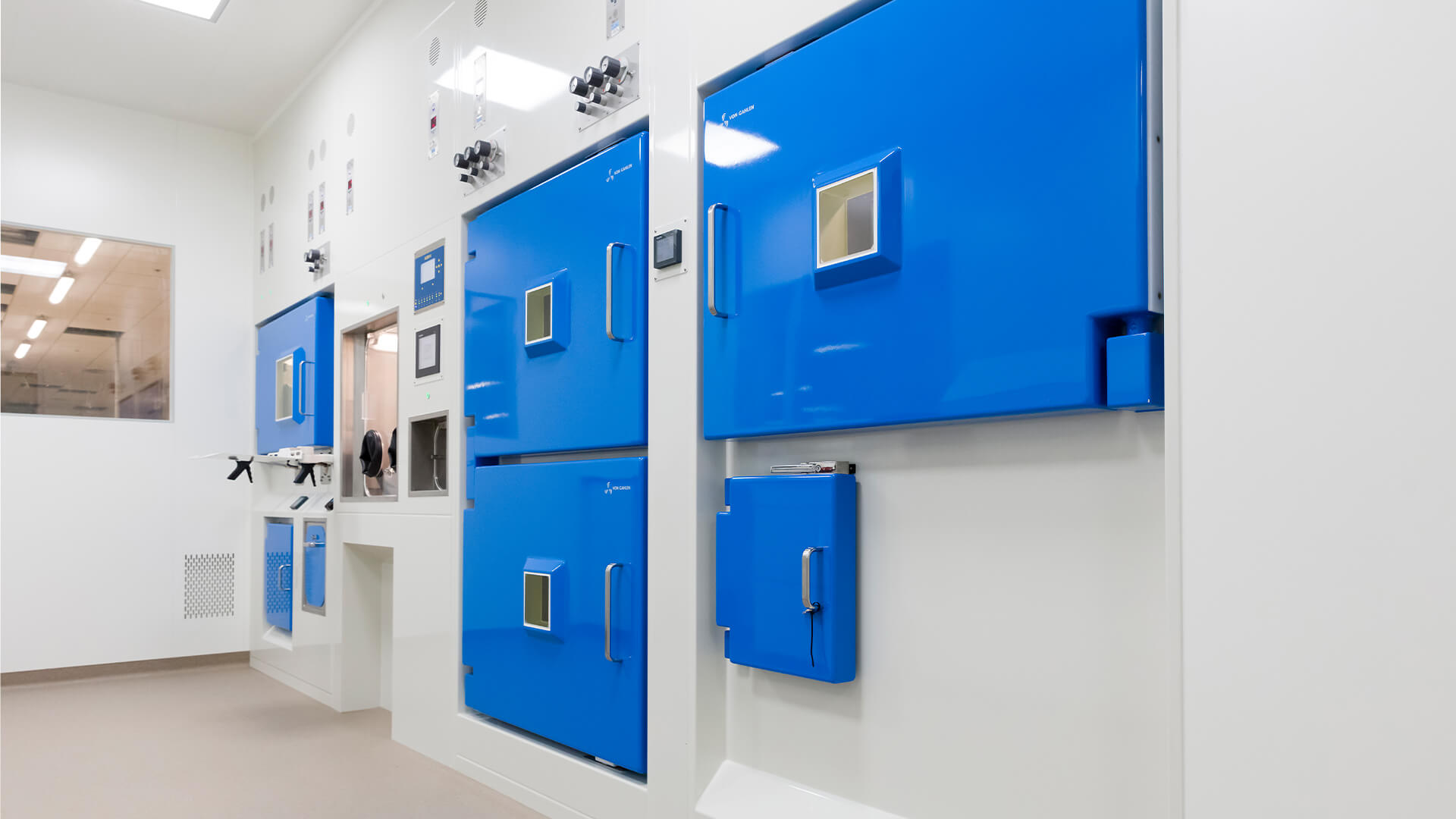
One of the four production lines at BV Cyclotron VU.
Quality and trustworthiness
“Quality is key in our line of work”, says Maria. “Sterile conditions are a 24/7 necessity. After all, a tracer will be inserted in a human vain in no-time. But quality is more than just hygiene. Von Gahlen brings the knowledge, experience
and expertise we needed. They won this tender based on their proven quality and trustworthiness. Their pragmatism simply makes things happen, no matter how much tailor-made work is required. There is no bluff and they simply do as they say. Also,
we were closely involved in every step of the process. We got to see every technical design and both the Factory Acceptance Test and the Site Acceptance Test were professionally prepared. The reports they deliver with the equipment are very complete
and detailed. This is obviously essential when GMP-auditors visit us."
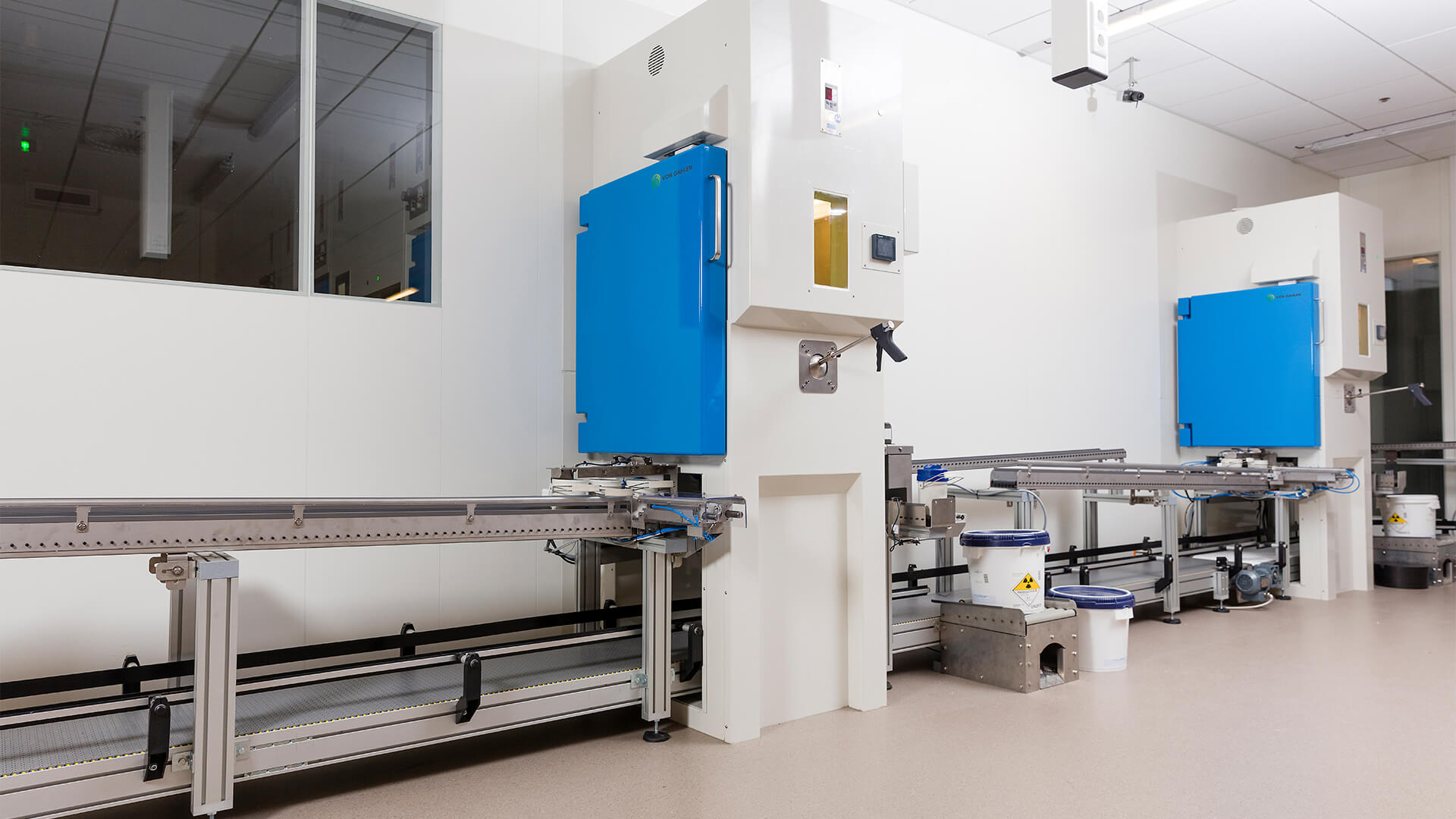
At the back of the hot cells the output, packaging and further transportation of PET radiopharmaceuticals and Zr-89 (Zirconium-89) takes place.
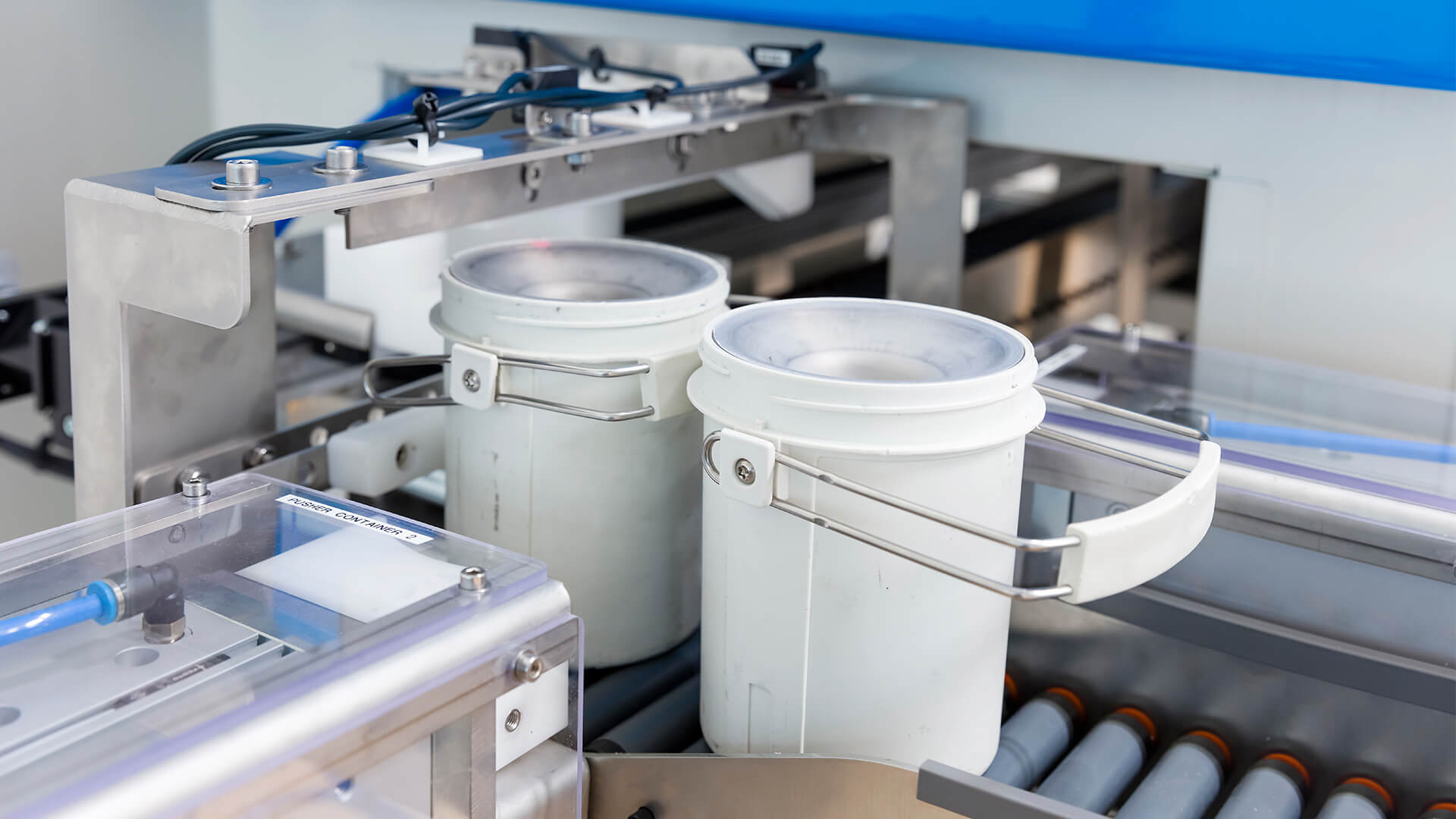
CHEMICAL CONNECTION
As we leave the basement and move up a few floors, we enter the territory of Bert Windhorst. He is a professor in radiopharmaceutical chemistry: the science of labeling molecules with radionuclides. Bert leads a research group that produces radioactive tracers for diagnosing purposes.
Radioactivity produced by BV Cyclotron VU finds its way up through the target lines to six hot cell suites tailor-made by Von Gahlen. In these hot cells the synthesis takes place, resulting in a wide range of tracers. “We are producing over one hundred products in relatively small batches. It goes without saying that it takes customization of the hot cells to comply with these varying production batches”, as Bert explains. He also gives an example of customization that sounds simple: "We make many different tracers and we need to be able to exchange the synthesis equipment inside the hot cell easily. The integrated tray is very helpful for that."
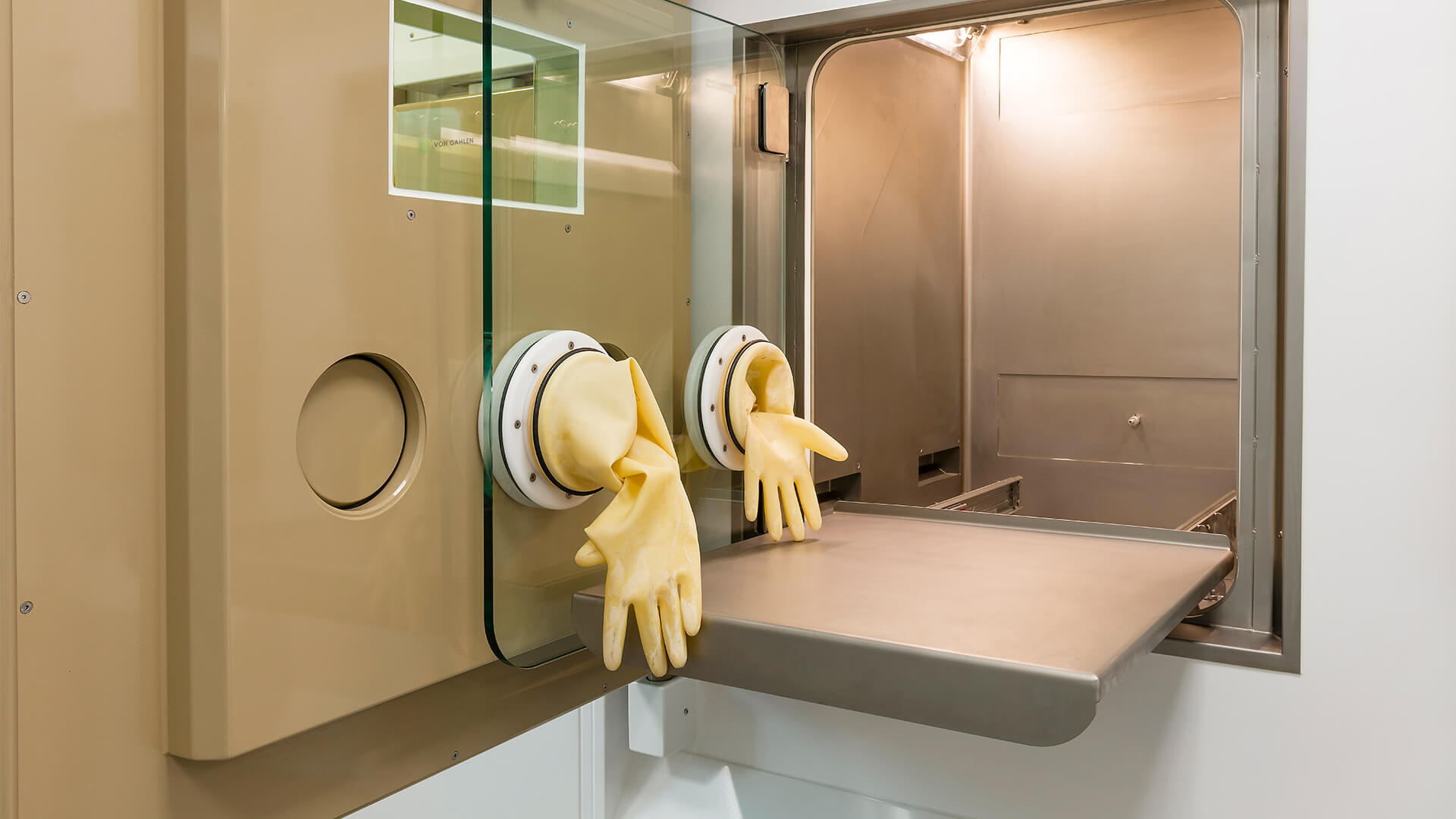
The tray: not as high tech as the rest of the cell, yet very convenient and user friendly.
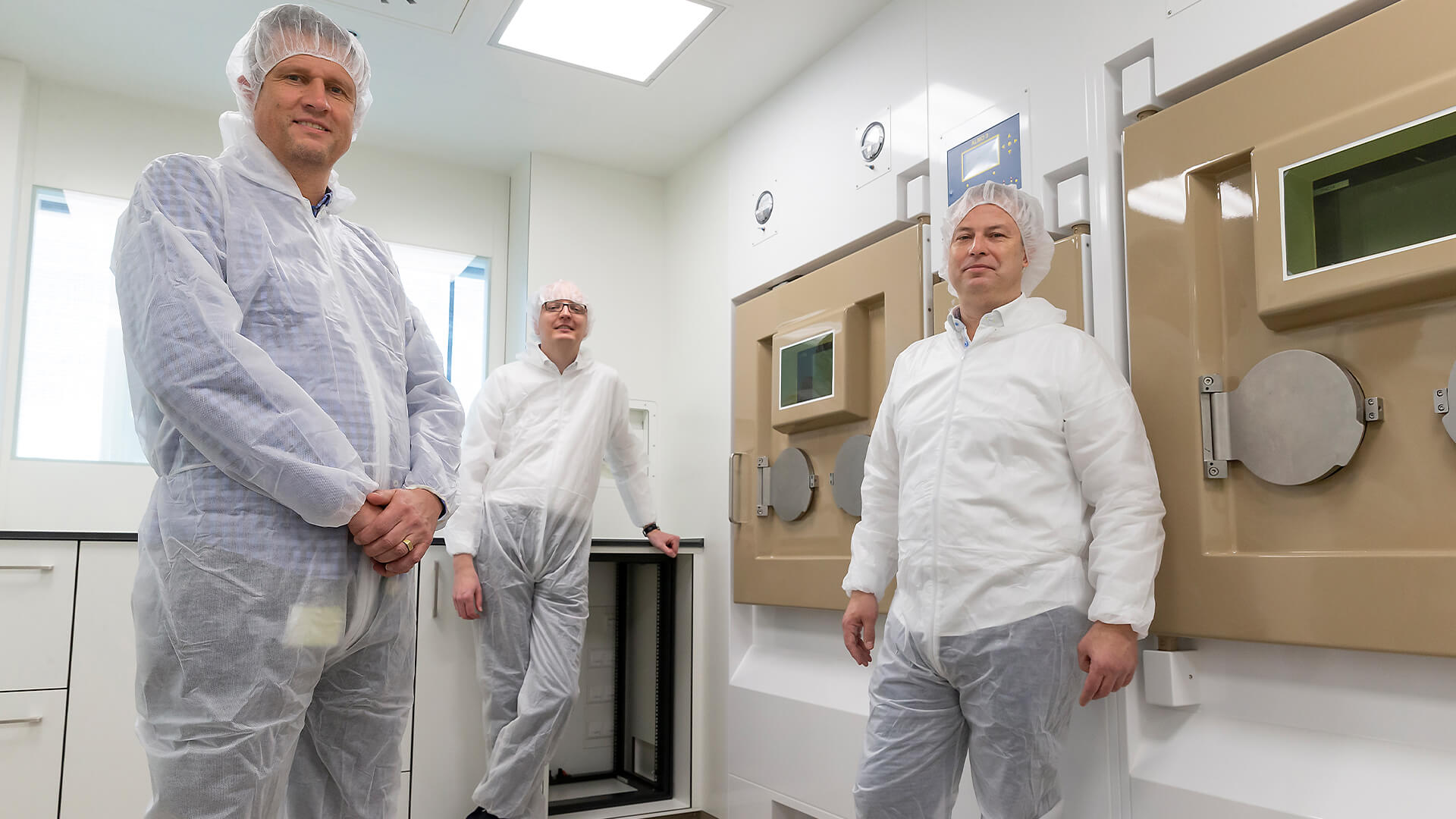
In one of the six hot cell suites, from left to right: Robert Schuit, Alex Duiker and Bert Windhorst.
Project management
“The six hot cells suites are completely integrated with the cleanrooms in which GMP is an obvious requirement. Once again, we had to come up with tailor-made solutions to make synthesis and dispensing of such a wide variety of products possible. The tender for this project involved multiple suppliers. Bert explains their choice for Von Gahlen: “Von Gahlen won the tender based on their designs and project management plan. It was a very interactive process. In particular the engineering sessions at Von Gahlen HQ in Zevenaar. Theo (Project Manager of Von Gahlen, red.) did not only focus on the hot cells. He oversees the entire building project and also coordinated the installation engineers throughout the installation phase. The protocols are very detailed so there is no room left for misunderstandings.”
The meaning of: for sure
The Von Gahlen pay-off is: for sure. These two words promise assurance, certainty and reliability. As Bert reviews his Von Gahlen experience: “Von Gahlen shows true dedication and a sharp eye for quality. Quality is in their products, in the use of materials and in the fine finishing touch. But also in their time management skills and the way they document the entire process, making the whole operation extremely transparent.”
PREPARATION OF SYRINGES
Bert closely cooperates with Robert Schuit. One of Robert’s responsibilities is the next step following the work of Bert and his team. This next step is the preparation of the actual administration of the radiopharmaceuticals to patients. Or as Robert illustrates: “Drawing up the right dose of the right radiopharmacon in a syringe. We label the syringe for the right patient and transport it to the clinic.”
This preparation process takes place in a lab that Robert and Von Gahlen together modelled and equipped with three shielded hoods. Two of the three hoods are Shielded Laminar Hoods (PET) and one is a Compact Technetium Solution. Since the latter processes technetium, it has an easy to operate, electrically elevated generator safe. This compact hood provides a sterile and safe environment for manipulations in low energy gamma applications. For high energy gamma applications we installed the two Shielded Laminar Hoods (PET), which provide an optimal combination of shielding and ergonomics and enables to prepare products in a sterile environment.
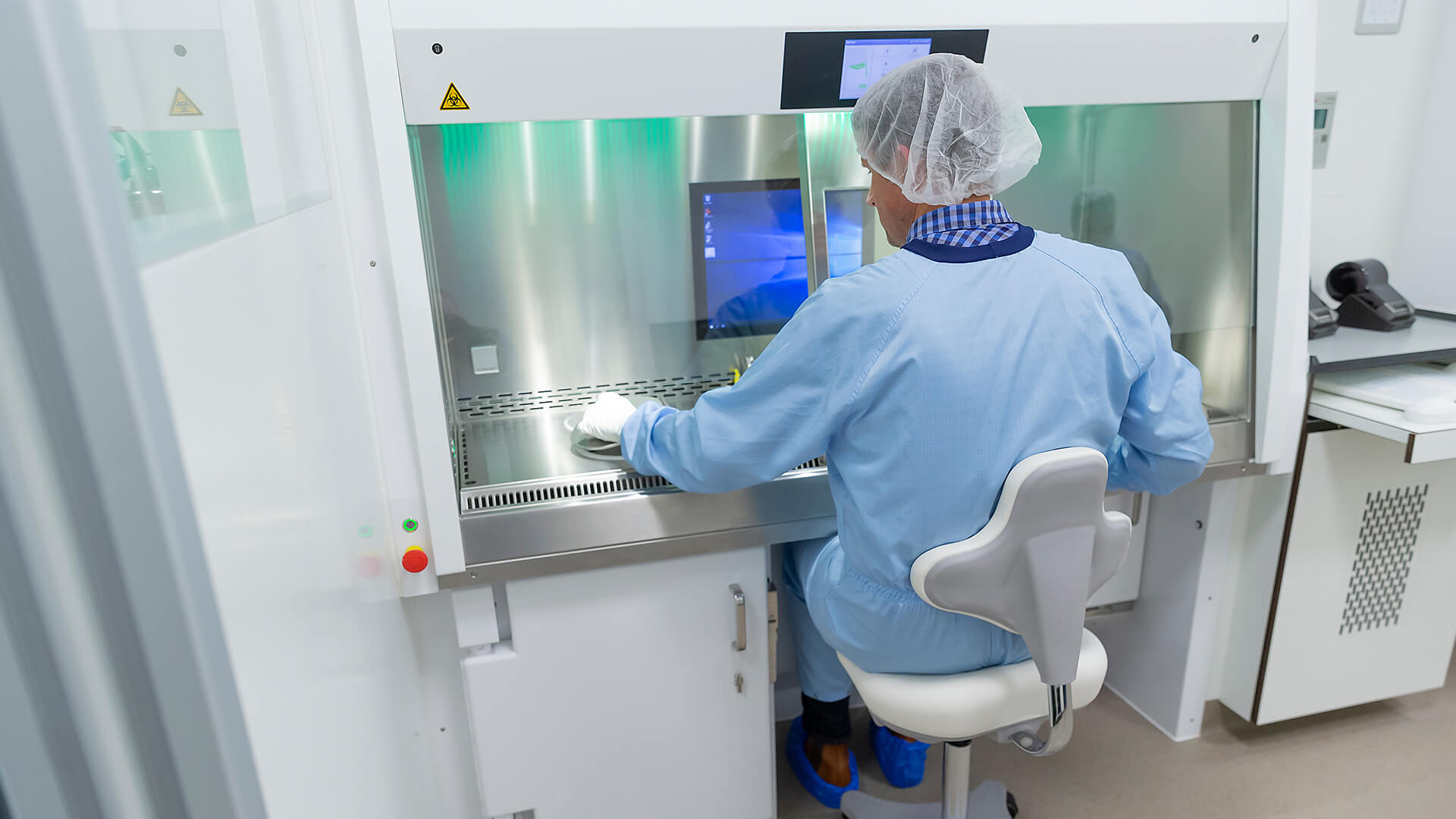
The Compact Technetium Solution with an integrated safe on the left below. From there, technetium compounds get electrically elevated into the shielded cabinet for further processing.
ADDING AN AUTOMATED DOSE DISPENSER
“Small, but clever and functional details can make a big difference in working with these kinds of materials. Von Gahlen offers those clever details”, says Robert. “We are an academic institute with a heavy research component. So we are dealing with more variation and specialties in nuclear medicine than, let’s say, the more regular research centers and hospitals. Apart from quality, flexibility is also a main factor in decision making. Von Gahlen is a dedicated partner and that is exactly what we need to find solutions for the flexible handling of our diverse productions.”
Von Gahlen also provided Robert’s department with an Automated Dose Dispenser. This product is specifically designed for high energy gamma applications (PET) and makes light work of the heavy syringe- and vial shields that are difficult to manipulate by hand. “This is a perfect addition to our syringe filling process. We can use it for almost all the tracers we produce”, concludes Robert.
PROUD PART OF A GLOBAL BENCHMARK
The Imaging Center draws attention from all over the world, since it is the only place in the world where production, treatment and research are brought together in one center. We are proud that our products and solutions are part of this center of excellence in biomedical imaging.
Would you like to know more about this project? Or do you want to know what we could provide for you?
Feel free to contact us.