Investing in a PET/CT scan
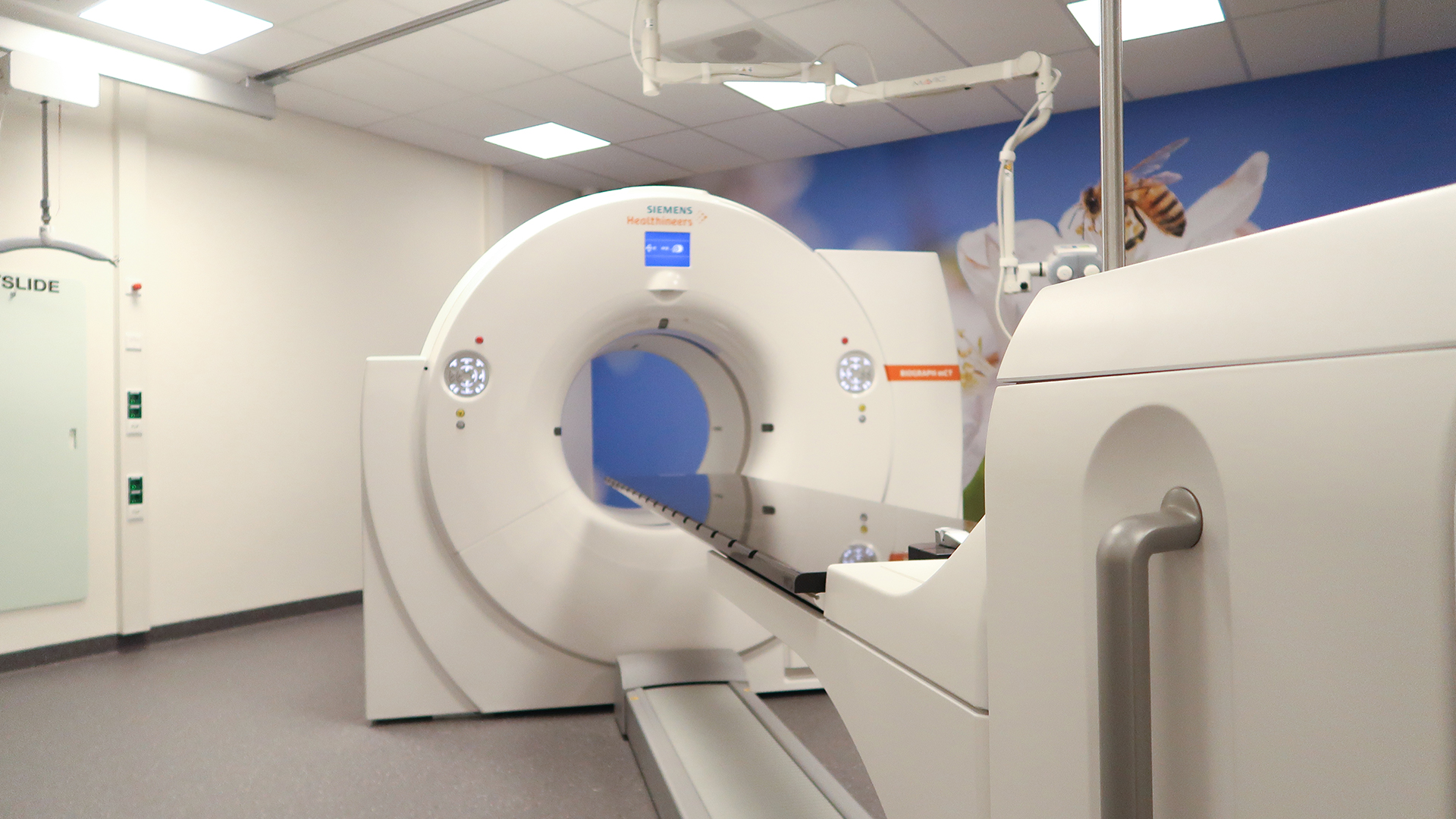
The brand new PET/CT scan at SKB Winterswijk.
Jenny kicks off by going back three years: “It all started with a business case to investigate the possibility of adding a PET/CT scan to our facility. Until recently we had to refer patients to other hospitals for diagnosing. Investing in a modern PET/CT scan and additional equipment turned out to be financially interesting, but also much more convenient for our patients. We don’t have to send them to hospitals further from their homes anymore. For financial reasons we also decided to go for in-house dispensing of Fluor-De(s)oxy-Glucose (FDG) by drawing up the right doses in syringes. The alternative would be purchasing complete and off-the-shelf syringes, but the long term expenses will be way too high. Especially when you add the transportation costs for such products. An extra benefit for our patients is the fact that we now have the flexibility to immediately dispense an extra dose if we urgently need to scan a patient.”
Adding Von Gahlen equipment
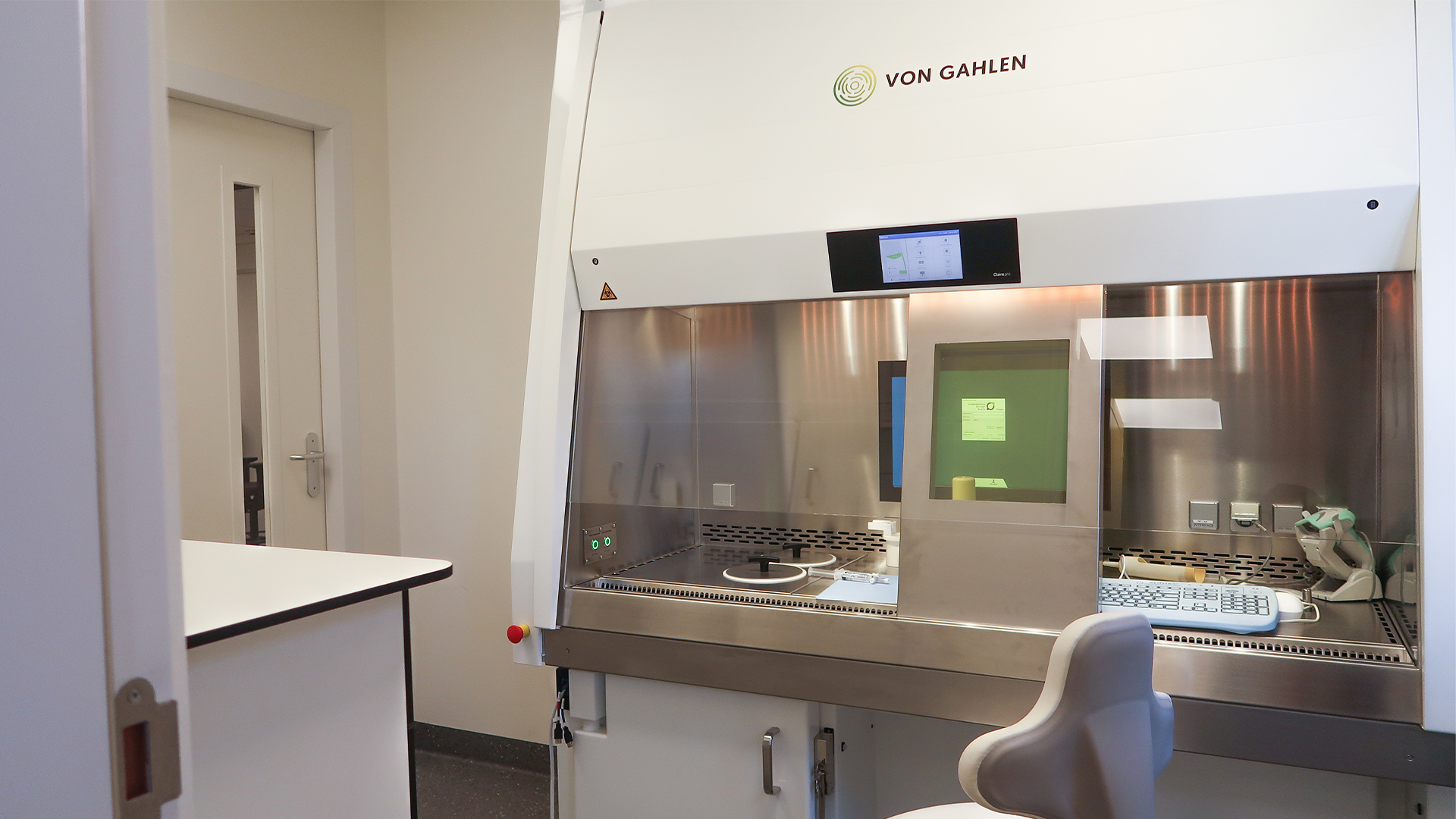
Von Gahlen’s Shielded Laminar Hood at SKB Winterswijk
“For that matter we installed a Shielded Laminar Hood – SPECT with a double, electrically elevated, generator safe for Technetium”, Arnod explains. “And since FDG radiation is relatively strong, we shielded the hood with 50 mm of lead instead of the regular 10 to 25 mm shielding. This makes this laminar hood specifically tailored for working both with Technetium as well as FDG. A customer specific solution, efficiently solving the challenges of working with both isotopes. We also tailor-made three shielded pass through hatches, which were integrated in the lab. This allows to safely pass on the syringe that Jenny prepares in the SLH, to the other side of the lab wall where Jenny’s colleagues can further transport the syringe to the patient. To do so, we also delivered the syringe carriers.”
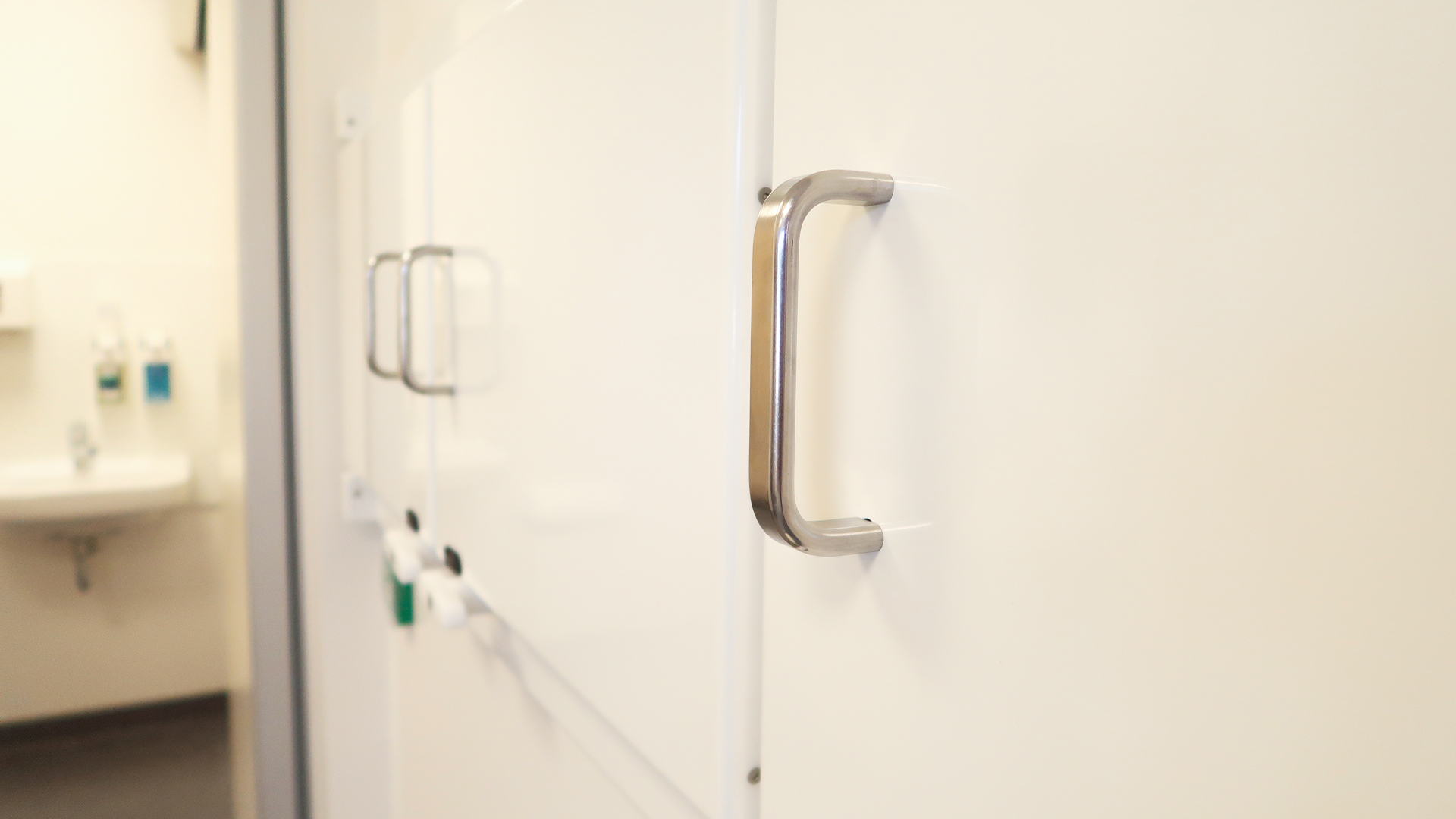
Three tailor-made shielded pass through hatches
A first time partnership
Although Von Gahlen and SKB are basically neighbors, this was the first time the two parties cooperated. “True, Von Gahlen wasn’t our regular supplier for products like these. But Von Gahlen is a local and that made me extra curious about what they had to offer. I approached three different suppliers and Von Gahlen turned out to be the most convincing one. They thought through the project very comprehensively, making Von Gahlen our obvious choice”, as Jenny clarifies.
Making sure to be for sure
Throughout the project Jenny mainly stayed in touch with Jerom and Lucas. The former was responsible for managing this project and the latter took the technical lead as engineer. Looking back on this cooperation, there is one particular thing that comes to Jenny’s mind: “Honestly, I wasn’t quite used to the highly protocolled way Von Gahlen works”. According to Arnod there is a reason for that: “Well, it’s not like delivering, let’s say, a washing machine. We also try to convince ourselves of the quality of our productions. It’s a customer specific product and we want to make absolutely sure that everything the customer asked for, is there and operational. ‘For sure’ isn’t just an expression. These protocols are there to prove it in writing.”
In relation to this, Jenny strongly recalls the site acceptance test. “I was already convinced when Von Gahlen decided to test an extra hour or so. “But”, as Jenny tells smiling, “don’t get me wrong, I definitely like this approach.”
Jenny and her team are now completely up and running and proud of this new chapter for SKB Winterswijk. Just like we are proud of us being part of this new chapter.
Would you like to know more about this project? Or do you want to know what we could provide for you?
Feel free to contact us.